The Importance of Mold and Tooling in Metal Fabrication
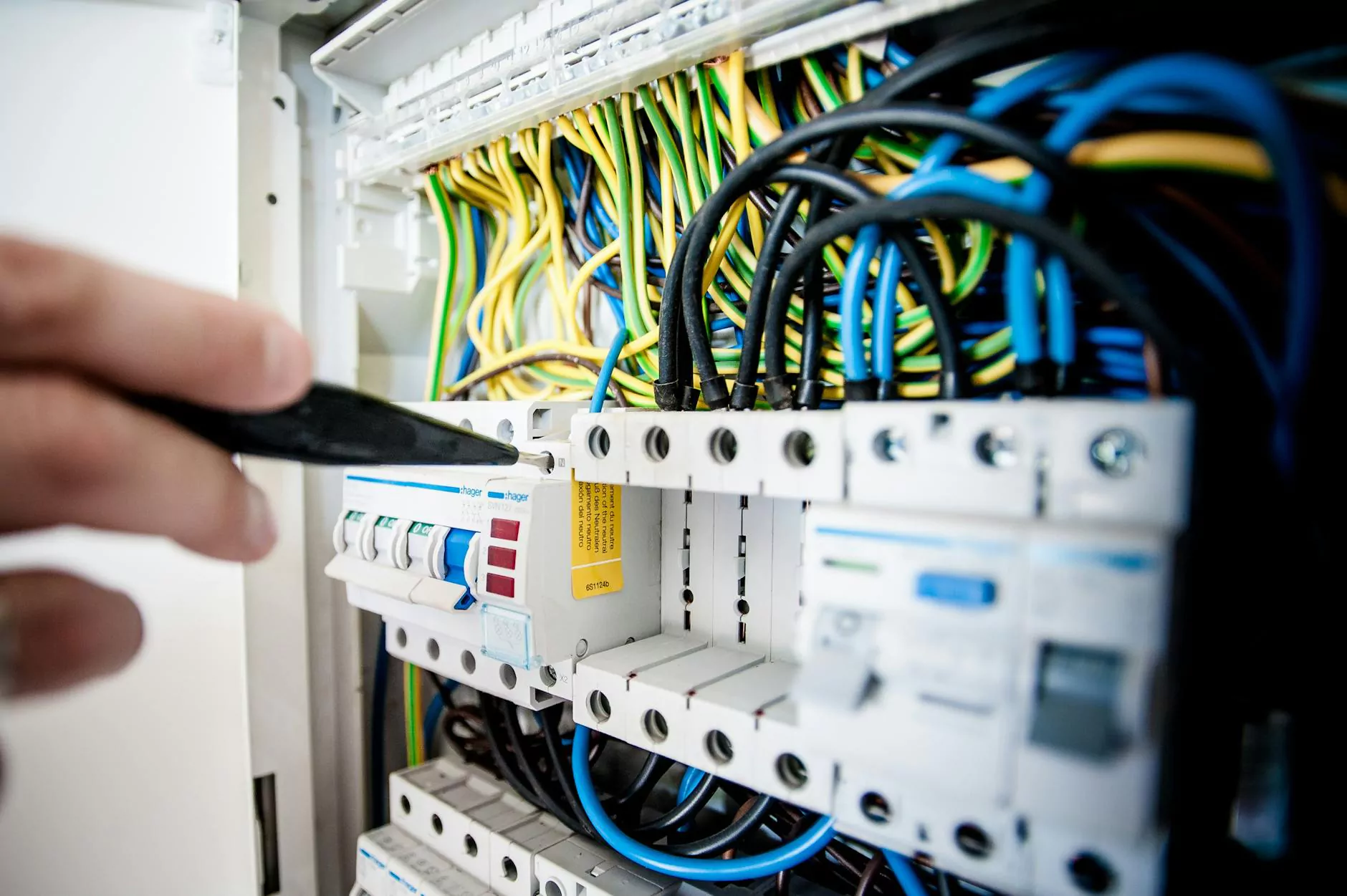
Metal fabrication is a cornerstone of numerous industries, undergirding the production of everything from intricate machinery to large-scale structural components. At the heart of metal fabrication lies a critical process known as mold and tooling. This article delves into the various aspects of mold and tooling, emphasizing its significance, methods, technologies, and innovations that drive the metal fabrication industry forward.
Understanding Mold and Tooling
Mold and tooling can be defined as the creation of tools and molds used in manufacturing processes to shape materials. These important elements are essential for producing parts with high precision and repeatability. In the realm of metal fabrication, effective mold and tooling lead to enhanced productivity and efficiency, yielding high-quality products while minimizing waste.
The Role of Molds in Metal Fabrication
Molds are designed to create specific shapes by allowing metal to cool and solidify in a predetermined form. Here are several key points regarding their role:
- Customization: Molds can be tailored to meet the specific requirements of a project, allowing for customization in design and function.
- Efficiency: Once a mold is completed, it can consistently produce parts at a rapid pace, significantly speeding up the manufacturing process.
- Precision: Molds ensure that each part produced meets exact specifications, reducing errors and enhancing quality control.
Types of Molds Used in Metal Fabrication
In the metal fabrication industry, several types of molds are utilized, including:
- Injection Molds: These are commonly used for producing complex shapes with intricate details, ideal for high-volume manufacturing.
- Die Cast Molds: These molds are employed to create metal parts using a die casting process, providing durability and precision.
- Blow Molds: These molds shape materials through a blowing process, typically used for hollow parts.
The Importance of Tooling in Mold Production
Alongside molds, tooling is imperative in the production of metal components. Tooling refers to the various tools that assist in manufacturing, impacting both the quality and efficiency of production.
Essential Components of Tooling
Tooling encompasses a wide range of equipment, including:
- Cutting Tools: Used to remove material from a workpiece to achieve the desired shape and finish.
- Forming Tools: These are critical in shaping and bending metal without cutting, which is vital in the production of complex geometries.
- Assembly Tools: Essential for putting together various components, ensuring that parts fit together seamlessly.
Tooling Techniques in Metal Fabrication
Tooling techniques are critical for the success of the mold and tooling process, with some key techniques including:
- Computer Numerical Control (CNC): CNC machines allow for automated control of machining tools, offering high precision and reducing the risk of human error.
- 3D Printing: Rapid prototyping using 3D printing technologies can significantly reduce lead times for tooling creation.
- EDM (Electrical Discharge Machining): Suitable for creating complex shapes in hard metals, EDM is vital for accurate mold manufacturing.
Benefits of Effective Mold and Tooling Processes
Effective mold and tooling processes are integral to the success of metal fabrication businesses. The advantages include:
- Cost Efficiency: High-quality molds and tools can reduce production costs by minimizing errors and waste, leading to significant savings over time.
- Improved Product Quality: Precision manufacturing leads to high-quality end products that meet client specifications and industry standards.
- Faster Production Times: Well-designed molds and tools enable quicker setup times and faster cycles of production, accelerating delivery to market.
- Innovation and Development: Advanced mold and tooling techniques foster innovation, allowing companies to develop new products and technologies.
The Future of Mold and Tooling in Metal Fabrication
The future of mold and tooling in metal fabrication is bright, with multiple trends on the horizon:
- Smart Manufacturing: Integration of IoT devices into the tooling process can monitor and optimize production, ensuring maximum efficiency.
- Sustainable Practices: Environmentally-friendly materials and processes will become increasingly important, pushing manufacturers to innovate.
- Custom Solutions: The demand for personalized products will drive the need for customized tooling solutions tailored to specific client needs.
Conclusion: Harnessing the Power of Mold and Tooling
In conclusion, the significance of mold and tooling in the metal fabrication industry cannot be overstated. These processes enable manufacturers to produce high-quality, efficient, and precise components essential for a plethora of applications. As technologies advance, businesses that invest in innovative tooling and molding techniques will undoubtedly gain a competitive edge in an increasingly global market.
At DeepMould.net, we are committed to delivering the best in mold and tooling solutions. Our expertise in metal fabrication ensures that we meet and exceed our clients' expectations by delivering optimized manufacturing solutions tailored to their needs. Explore our services and discover how we can enhance your production capabilities today!