Automatic Label Applicators: Streamlining Your Business Operations
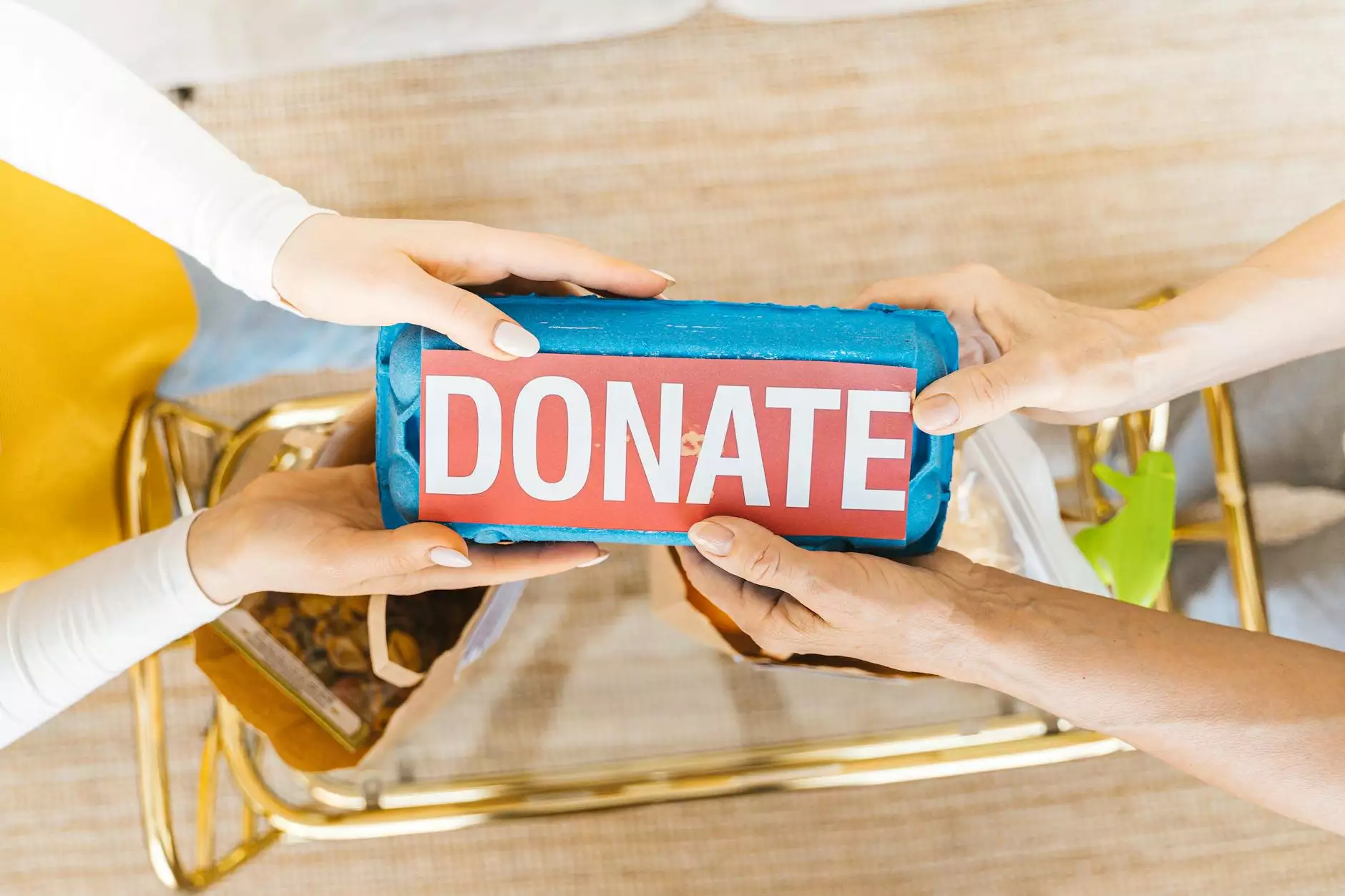
In today’s fast-paced business environment, efficiency and precision are crucial for success. One area that often requires significant improvement is the labeling process. This is where automatic label applicators come into play. These advanced machines can dramatically enhance production speed and ensure the accuracy of labels applied to products. In this article, we will explore the significance of automatic label applicators in various industries, discuss different types available, and provide insights on how to select the best one for your business needs.
Understanding Automatic Label Applicators
At its core, an automatic label applicator is a machine designed to apply labels on products quickly and efficiently. These machines are essential in industries ranging from manufacturing to retail, aiding in product identification, tracking, and marketing. With the capability to automate the labeling process, businesses can save time, reduce labor costs, and minimize human errors.
The Significance of Automatic Label Applicators in Business
Implementing automatic label applicators can significantly enhance operational efficiency and effectiveness. Here are key reasons why businesses should consider adopting these technologies:
- Increased Speed: Automatic label applicators can label products much faster than manual methods. This increase in speed translates to higher production rates, enabling businesses to meet customer demands swiftly.
- Enhanced Accuracy: Precision is paramount in labeling. Automatic systems reduce the risk of mislabeling, ensuring that every product receives the correct label.
- Cost Savings: By minimizing labor costs and reducing waste from labeling errors, these machines lead to significant cost savings over time.
- Improved Compliance: For industries that must adhere to strict labeling regulations, automatic label applicators help ensure compliance by automating font size, label placement, and necessary information.
- Better Brand Image: Consistency in labeling reflects professionalism, enhancing a company’s brand image. It demonstrates attention to detail and quality control.
Types of Automatic Label Applicators
Choosing the right type of automatic label applicator for your business depends on various factors, including the nature of the products, production volume, and specific labeling requirements. Here are some of the most common types:
1. Bottle Label Applicators
Bottle label applicators are designed specifically for cylindrical containers, such as bottles and jars. They can apply labels around the entire circumference of the product quickly and accurately. These machines are widely utilized in the beverage, food, and cosmetics industries.
2. Flat Surface Label Applicators
For products with flat surfaces like boxes or bags, flat surface label applicators are ideal. These machines ensure that labels are applied smoothly, without bubbles or wrinkles, which is crucial for aesthetic appeal and functionality.
3. Top & Bottom Label Applicators
Some businesses require labels on both the top and bottom of their products. Top and bottom label applicators allow for simultaneous labeling, streamlining the packaging process and enhancing efficiency.
4. Custom Label Applicators
For unique products with specific labeling needs, custom label applicators can be engineered to meet those requirements. These machines are tailored to fit particular product shapes, sizes, and labeling techniques.
Benefits of Using Automatic Label Applicators
The advantages of integrating automatic label applicators into your business processes extend beyond basic functionality. Here are additional benefits:
A. Increased Productivity
With the ability to operate continuously without breaks, automatic label applicators significantly boost productivity. They maximize output, allowing businesses to scale operations effectively to meet demand.
B. Flexibility
Modern automatic label applicators are highly versatile, accommodating a range of label types, sizes, and materials. This adaptability makes it easier for businesses to pivot based on changing industry trends or product lines.
C. Reduced Waste
By ensuring accurate label application, businesses can drastically cut down on wasted materials. This reduction in wastage not only saves money but also promotes environmentally friendly practices.
D. User-Friendly Operations
Most automatic label applicators come equipped with intuitive controls, making them easy to operate without extensive training. This ease of use allows businesses to integrate them into existing workflows seamlessly.
Choosing the Right Automatic Label Applicator
When considering the purchase of an automatic label applicator, several factors should be taken into account:
- Product Dimensions: Measure the size, shape, and weight of your products, as this will determine the type of applicator you need.
- Production Volume: Assess your production speed requirements to choose an applicator capable of handling your volume efficiently.
- Label Specifications: Consider the types of labels you will be using, including material, size, and adhesive type.
- Integration: Ensure the applicator can integrate well with your existing packaging or production line.
- Budget: Establish a budget that takes into account not only the upfront purchase cost but also maintenance and operational expenses over time.
Best Practices for Implementing Automatic Label Applicators
Once you have chosen the right automatic label applicator for your business, implementing it effectively is crucial for maximizing its potential:
1. Proper Training
It’s essential that your staff receives comprehensive training on operating the new machinery. This training should cover maintenance, troubleshooting, and efficiency optimization strategies.
2. Regular Maintenance
To ensure longevity and efficiency, establish a routine maintenance schedule for your automatic label applicator. Keeping the machine in prime condition will prevent costly breakdowns and ensure consistent labeling quality.
3. Monitor and Adjust
After deploying the equipment, monitor its performance closely. Be prepared to adjust configurations or processes to ensure that labeling remains efficient and accurate.
4. Stay Updated on Technology Trends
The world of labeling technology is always evolving. Stay informed about the latest advancements and consider upgrades that could further refine your labeling process.
Conclusion
In conclusion, automatic label applicators are indispensable tools that bring about transformative efficiency and accuracy to various business operations. By integrating these machines into your workflow, you can anticipate a remarkable improvement in productivity, cost savings, and overall operational efficiency. As businesses face increasing competition and pressure to deliver high-quality products rapidly, investing in automatic labeling solutions becomes not only a strategic choice but a necessity for staying ahead in the marketplace. Explore the options available at your trusted provider, like Omega Brand, and revolutionize your labeling processes today!