Exploring the Impact of Plastic Injection Moldings on Modern Business
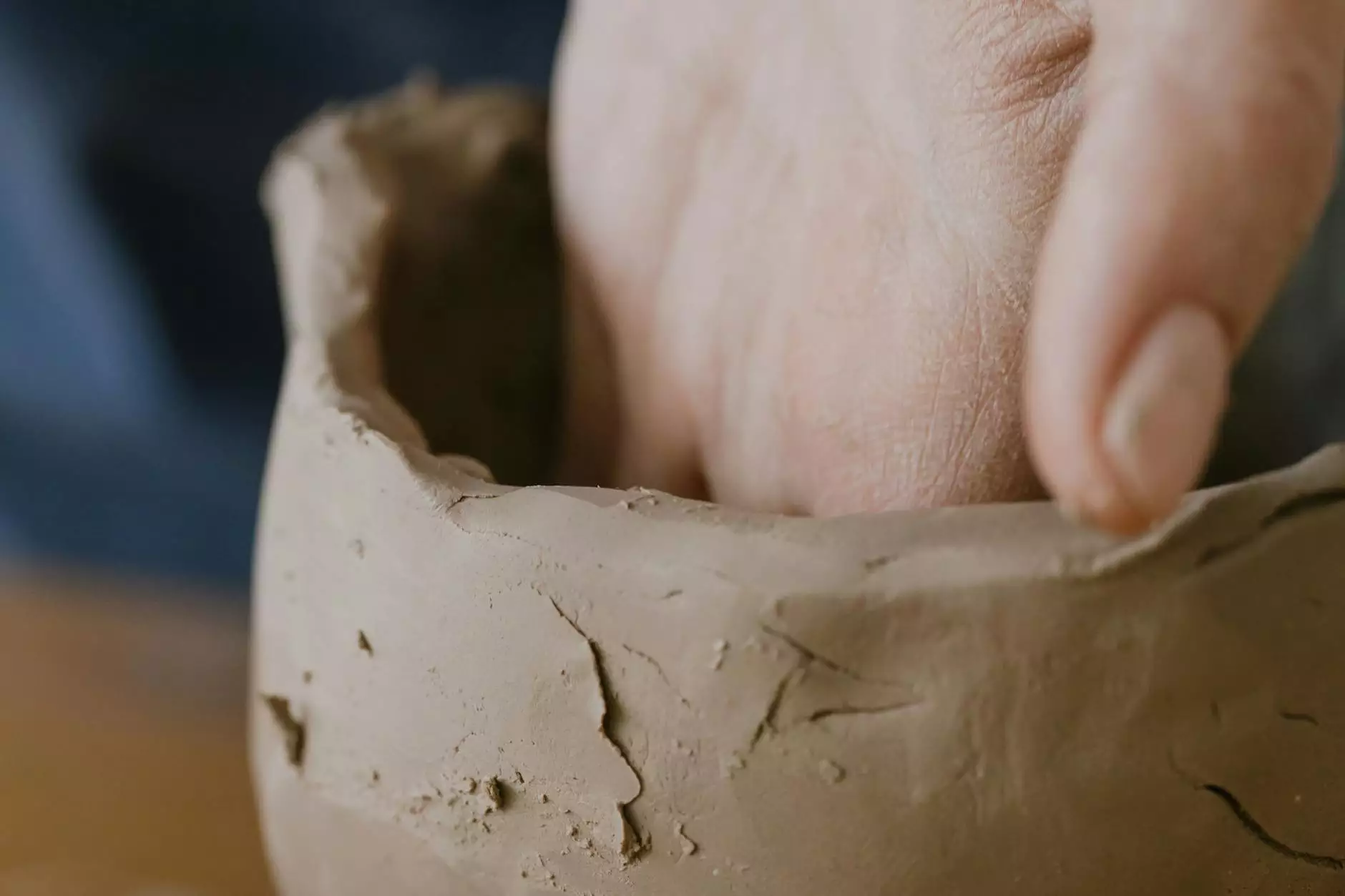
Plastic injection moldings are transforming the landscape of manufacturing and business operations across various sectors. As a cornerstone of production, this innovative process employs advanced technology to produce high-quality components with precision and efficiency. In this article, we will delve into the intricate world of plastic injection moldings, examining their applications, benefits, and their pivotal role in shaping contemporary industry standards.
The Basics of Plastic Injection Moldings
Understanding the essence of plastic injection moldings is crucial for any business considering implementing this technology. Essentially, plastic injection molding is a manufacturing process that involves:
- Melting plastic pellets and injecting them into a mold under pressure.
- Allowing the material to cool and solidify into the desired shape.
- Removing the finished product from the mold for further processing or assembly.
This method is celebrated for its ability to produce highly detailed and complex parts quickly, making it a favorite among manufacturers.
Why Choose Plastic Injection Moldings for Your Business?
The advantages of using plastic injection moldings in business are numerous, offering a competitive edge in today’s fast-paced market. Here are some key benefits:
1. Cost-Effectiveness
Once the initial mold is created, the cost per unit for mass production significantly decreases. This efficiency translates into lower overall production costs and makes plastic injection moldings a financially viable option for manufacturers.
2. High Precision and Flexibility
Plastic injection molding allows for extraordinary precision in manufacturing, producing components that meet stringent specifications. This flexibility makes it suitable for various industries, including:
- Automotive
- Consumer Electronics
- Medical Devices
- Packaging
- Household Goods
3. Rapid Production Rates
One of the standout features of plastic injection moldings is its capability to produce large quantities in a short time frame. This rapid production is essential for businesses that need to meet market demand quickly and efficiently.
4. Design Versatility
Designers can create intricate shapes and configurations that would be difficult or impossible to achieve with other manufacturing methods. This versatility allows businesses to innovate and differentiate their products in a crowded marketplace.
Applications of Plastic Injection Moldings in Various Industries
The reach of plastic injection moldings extends far beyond traditional manufacturing. Let's take a closer look at how this technology is applied in various sectors:
Automotive Industry
The automotive industry has been quick to adopt plastic injection moldings for parts such as dashboards, panels, and housings. The lightweight nature of plastic contributes to fuel efficiency while maintaining safety standards.
Consumer Electronics
In consumer electronics, plastic injection moldings enable the creation of complex shapes and components that enhance product functionality and aesthetics. Devices such as smartphones and laptops utilize various molded parts, from casings to battery compartments.
Medical Sector
The medical industry relies heavily on plastic injection moldings to produce precise and sterile components used in devices, instruments, and disposable items. These parts must comply with stringent regulatory requirements, making quality control essential.
Packaging Solutions
Packaging benefits from the efficiency of plastic injection moldings, allowing companies to create practical and visually appealing containers that protect products while enhancing shelf appeal.
Environmental Considerations in Plastic Injection Moldings
As the world increasingly prioritizes sustainability, businesses leveraging plastic injection moldings must also consider their environmental impact. Innovations in biodegradable plastics and recycling initiatives aim to address these challenges:
Using Recycled Materials
Many companies are turning to recycled plastics in their injection molding processes. This not only reduces waste but also helps companies market their products as environmentally friendly.
Developing Sustainable Practices
By investing in energy-efficient machinery and adopting practices that minimize waste during production, businesses can reduce their carbon footprint while maintaining high productivity.
Choosing the Right Partner for Plastic Injection Moldings
When selecting a plastic injection molding provider, businesses should consider several key factors to ensure they choose the right partner:
1. Experience and Expertise
The provider's experience in the industry can significantly impact the quality of the final product. Look for a company that has a proven track record in plastic injection moldings.
2. Advanced Technology
Ensure the manufacturer utilizes the latest technology and practices in injection molding to guarantee high-quality results, efficiency, and innovation.
3. Quality Control
A robust quality control process is essential for ensuring that each part produced meets your standards and is compliant with industry regulations.
4. Customer Service
Good communication and customer support can enhance the partnership experience, making it easier to address issues and collaborate on projects.
Conclusion: The Future of Business with Plastic Injection Moldings
As we navigate through the complexities of modern commerce, plastic injection moldings stand out as a transformative technology that empowers businesses to innovate, reduce costs, and meet consumer demands effectively. Companies like Deepmould.net are leading the charge, providing high-quality solutions that adapt to the evolving needs of various industries.
By understanding the potential applications, benefits, and best practices associated with plastic injection moldings, organizations can position themselves at the forefront of their respective markets, ensuring sustainable growth and success in the years to come.