Low Pressure Casting: An Essential Approach in Modern Manufacturing
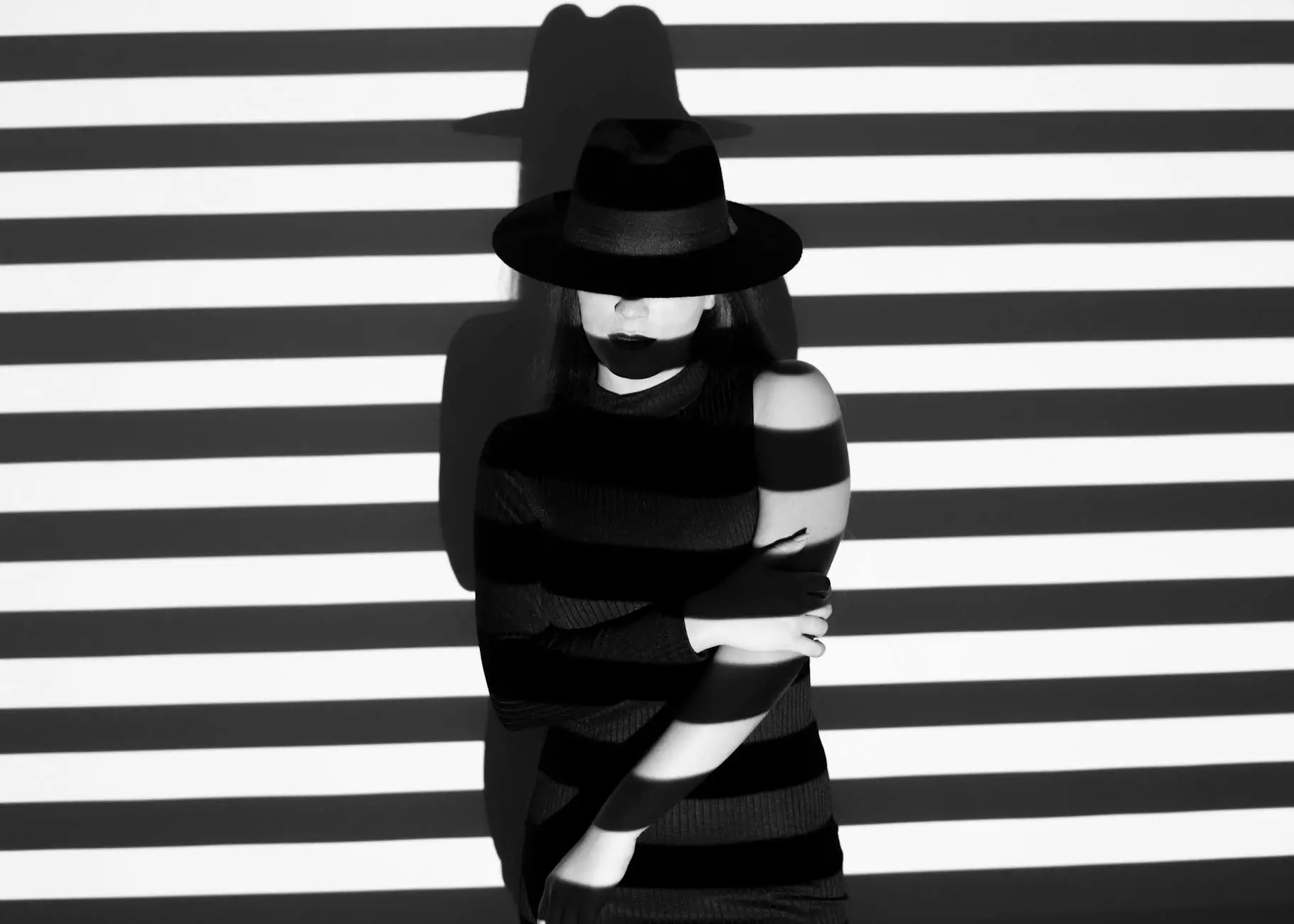
In the ever-evolving landscape of manufacturing, low pressure casting stands out as a game-changing technique that offers significant advantages, particularly in the realms of product design and 3D printing. This method combines efficiency with quality, making it a preferred choice for many businesses today. In this article, we will explore the concept of low pressure casting, its applications, benefits, and its relevance in art supplies and manufacturing processes.
Understanding Low Pressure Casting
Low pressure casting is a manufacturing process where molten metal is injected into a mold under low pressure, typically ranging between 0.5 to 2 bar. This process is particularly effective for creating complex shapes with high precision. By utilizing this method, manufacturers can achieve finer details in their products and improve overall quality control.
The Process of Low Pressure Casting
The low pressure casting process involves several critical steps:
- Mold Preparation: Molds are created with precise specifications, often using materials that can withstand high temperatures.
- Melting the Metal: The chosen alloy is heated until it reaches a molten state, ready for casting.
- Injection: Molten metal is injected into the mold under controlled low pressure. This minimizes air entrapment, resulting in a denser product.
- Cooling and Solidification: The metal is left to cool and solidify, taking the form of the mold.
- Mold Removal: Once cooled, the mold is removed, revealing the cast part, which may undergo further finishing processes.
Advantages of Low Pressure Casting
Low pressure casting offers numerous benefits that make it a desirable option for businesses:
- Enhanced Quality: The controlled environment reduces defects such as air pockets, leading to a denser and stronger final product.
- Cost-Effectiveness: With less waste material and reduced need for rework, businesses can save significantly on production costs.
- Complex Shapes: The technology allows for intricate designs that traditional casting methods may struggle to achieve.
- Fast Production Rates: Quick cycle times mean faster turnaround for products, improving overall efficiency and meeting market demands.
Applications of Low Pressure Casting
Low pressure casting is widely applicable across various industries, including:
- Automotive Industry: Components such as engine blocks and transmission parts benefit from the durability and precision of low pressure cast products.
- Consumer Goods: Everyday products, from kitchenware to electronic housings, leverage low pressure casting for enhanced design and functionality.
- Aerospace: High-performance aerospace components, which need to meet strict regulations, find low pressure casting to be indispensable for creating lightweight, yet strong parts.
- Art Supplies: In the artistic domain, low pressure casting is used for making moldings and prototypes, offering artists the opportunity to explore innovative designs.
The Role of Low Pressure Casting in Product Design
In product design, the low pressure casting technique facilitates rapid prototyping and iteration. Designers can quickly create high-quality prototypes that accurately reflect their vision, allowing for testing and adjustments before mass production. This reduces the time and cost associated with product development.
Innovative Materials and Techniques
Advancements in materials science have expanded the range of alloys suitable for low pressure casting. Designers can now select from a variety of metals with specific properties tailored to their projects, enhancing performance and aesthetic appeal. This versatility makes low pressure casting an ideal solution for industries that require both functional and visually appealing products.
Low Pressure Casting in 3D Printing
3D printing has revolutionized manufacturing, and when combined with low pressure casting, the results can be stunning. The ability to quickly 3D print a mold for casting allows for short runs of complex designs at a fraction of the traditional costs. Through this synergy, businesses can produce customized parts and explore unique designs that were previously thought impractical.
Sustainability and Low Pressure Casting
As businesses increasingly prioritize sustainability, low pressure casting emerges as an eco-friendly option. The process generates minimal waste and is conducive to recycling materials, significantly reducing the environmental impact. Additionally, the durability of cast products often means a longer lifecycle, contributing to eco-conscious consumption patterns.
Reducing Carbon Footprint
By employing energy-efficient practices in the melting and casting processes, businesses can further reduce their carbon footprint. Low pressure casting setups can be optimized for lower energy consumption, which is essential in today’s environmentally aware market.
Conclusion: Embracing Low Pressure Casting for Future Success
In conclusion, low pressure casting is more than just a manufacturing technique; it is a bridge to innovation, quality, and sustainability. For businesses looking to enhance their product design capabilities and streamline production, implementing low pressure casting can lead to significant benefits. At arti90.com, we believe in the transformative power of this technique and encourage industries to explore its vast potential.
Whether you are in the automotive sector, consumer goods industry, or a creative field like art supplies, low pressure casting can elevate your business to new heights. Embrace the future of manufacturing and harness the benefits that low pressure casting can bring to your operations.